There are similarities and differences between the mills that are most commonly used for commercial phosphate grinding. The following insight into the performance variables across the mill types helps to determine which mill is the right fit for specific phosphate grinding applications.
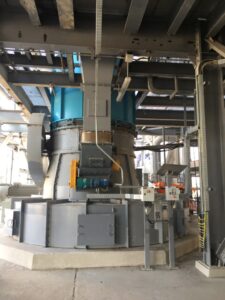
A brief introduction of 3 common mill types:
- Ball Mills – a horizontal rotating cylinder containing a charge of steel balls. The balls tumble as the mill turns and material caught between the balls is ground to powder.
- Table-Roller Mills – a horizontal table rotates with spring-loaded rollers mounted above. Material fed into the center of the table passes underneath the rollers and is ground to powder.
- Pendulum-Roller Mills – vertical rollers rotate inside a fixed horizontal ring. Material fed between the rollers and ring is ground to powder.
Similarities across the mills:
All 3 mill types require a continuous controlled feed, regulated to keep optimum conditions. This is done by selecting a suitable variable to control – noise is the standard method for ball mills; motor amps or pressure drop are used for roller mills. Also, all phosphate mills operate as air swept systems, using air to remove fine particles from the grinding zone to reduce the cushioning effect that they exert. This allows the grinding action to be concentrated on the large oversize particles, and is the key to efficient milling.
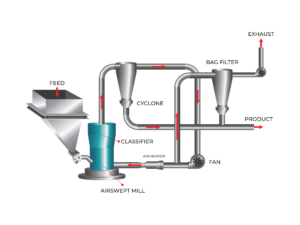
Milling efficiencies:
The mill efficiency depends upon effective air sweeping of the grinding zone, and the tumbling charge in a ball mill cannot be airswept very well. This is why a ball mill will always produce excessive fines and be less efficient than a roller mill. The pendulum-roller mills have a fluidized bed of material in the grinding zone, so fine particles are air swept from the mill as soon as they are made. This gives a narrower size distribution than the table mill, and improved grinding efficiency. The table-roller mills are not far behind.
Air classification:
The mill air circuit is the same for any mill and is designed to maximize the air sweeping effect. The high airflow needed to ensure all fines are swept from the grinding zone also carries some oversize particles, so a separator is needed to return these to the mill. The product size particles are then removed from the conveying air in cyclones and bag filters. The airflow depends only on the milling rate so similar capital and operating costs apply to every type of mill, and selection of the type of mill is therefore the critical factor.
The variables to consider are:
- Capital cost – ball mills are always more expensive to buy and install
- Power cost – ball mills always use most power, as the whole mill rotates, not just the grinding elements
- Wear cost – ball mills are always cheaper because the grinding media are un-machined castings and can be replaced without stopping the mill.
Plant Capacity:
Another consideration is the capacity of the plant – large capacity roller mills are a recent development, and previously a single stream ball mill line was comparable in capital cost to a multiple roller mill installation.
For most projects, the choice depends upon the cost of electricity and the abrasiveness of the material being ground. If the rock is abrasive and power is cheap then a ball mill would be preferred, if wear rates are not excessive and power is expensive then roller mills would be best.
However, the high capital cost of the ball mill means that the abrasion rate must be quite high to justify the extra cost, and even for cement clinker there is a trend away from ball mills to reduce power costs.
Thus, the nature of the material to be ground is critical, and for phosphates we can generalise as follows:
- Commercial sedimentary phosphates have low silica content and are easy to grind, so a roller mill is usually the most economic choice
- Low-grade indigenous phosphates have high silica content and high wear costs but are usually in places where power is expensive and so roller mills are predominant
- Igneous apatites are very abrasive and are typically found in locations where power costs are relatively low, so usually ball mills are used for this duty.
The above comments apply to dry grinding; wet grinding makes wear rates so high that only ball mills can be considered.
When it is determined that a roller mill is the best option for a particular project, the choice is between table and pendulum mills.
For mill sizes up to 600kW the pendulum-roller mills are generally most economic, but above this size the table-roller mills can be competitive.
Contact Us to learn more about why the pendulum roller mill may be right for your phosphate grinding application.