Options for Improvement in Air Classification
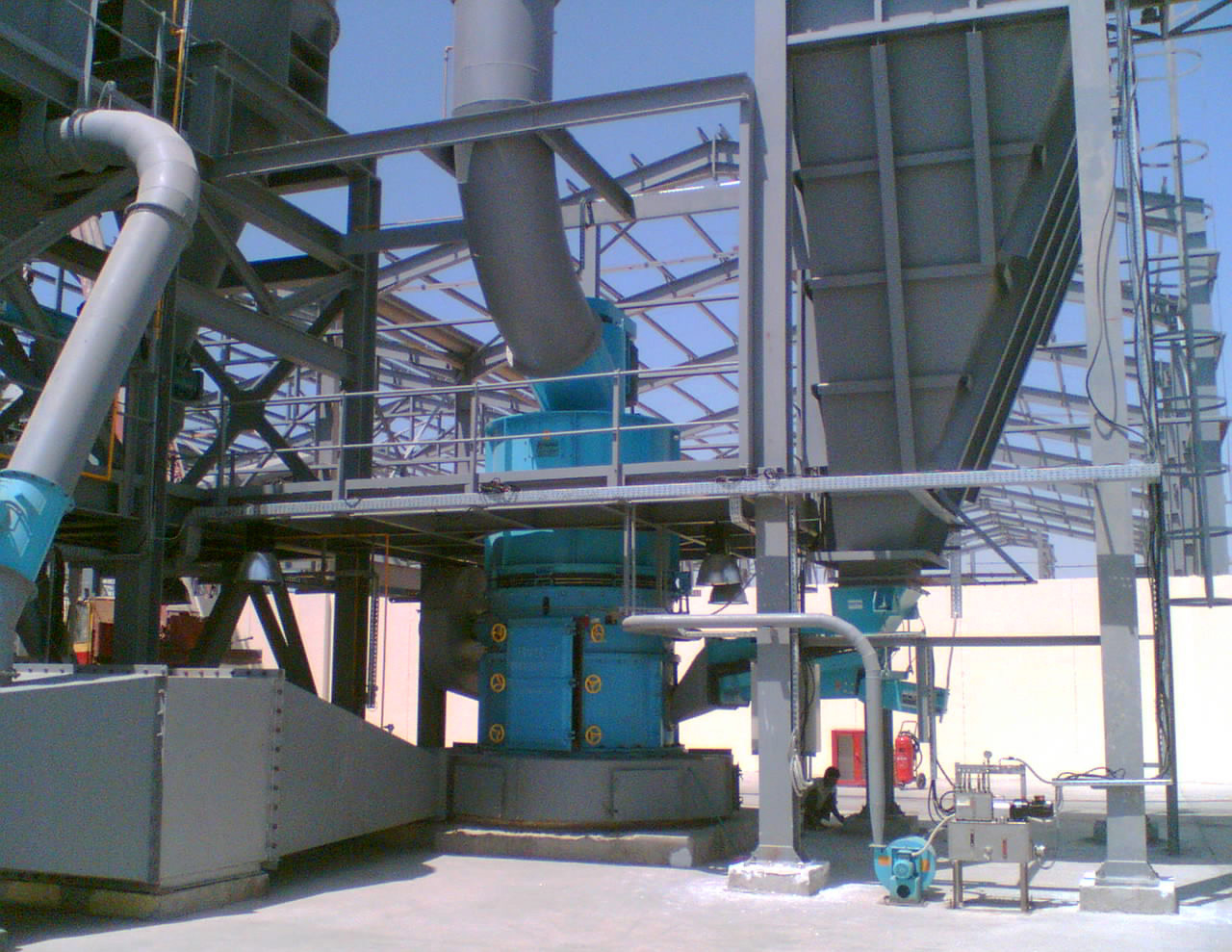
Air classifiers are essential for controlling the product size, particle recirculation, power consumption, and overall profitability of an airswept mill system. Several different types of classifiers are available with each having its optimal performance ranges and applications. Classifier selection and performance optimisation are critical as they directly impact overall fertilizer mill system performance and efficiencies. Ongoing advances in classification technology are leading to further enhancements in yields and efficiencies.
An Introduction to Air Classifiers
Fine grinding of hard, friable material such as phosphate rock with an air-swept mill involves the continuous return of oversize material to the mill’s grinding zone for further reduction until the desired size is met. It is the role of the classifier to control both the amount of recirculation inside the mill and the particle-size distribution of the end product, with changes in a classifier’s settings having direct effects on the milling system’s power consumption, capacity, vibration, and product size distribution.
Essentially, the classifier functions as the controls of the grinding circuit, determining both the material that should exit the mill as correctly sized product as well as what should be returned for reprocessing.
There are four main mill classifier types:
- Static classifiers: these are fixed volumetric classifying devices with lower maintenance requirements, however, increases in fan volume will directly increase particle size and decrease cut efficiencies.
- Dynamic classifiers: most commonly found in fertilizer applications, these incorporate a rotating rotor vane to enhance particle classification and, consequently, have a wider operational range.
- High efficiency classifiers: ideal for cement applications, these combine useful elements from both of the above technologies by using a static set of vanes to guide the airflow into a rotating rotor, alongside other optional features for higher level of particle control.
- Divorced classifiers: also common in fertilizer applications where very fine particles (<45 μm) are specified. Divorced classifiers take particle recirculation outside of the mill’s airstream and provide the opportunity to efficiently generate multiple product sizes from a single feed.
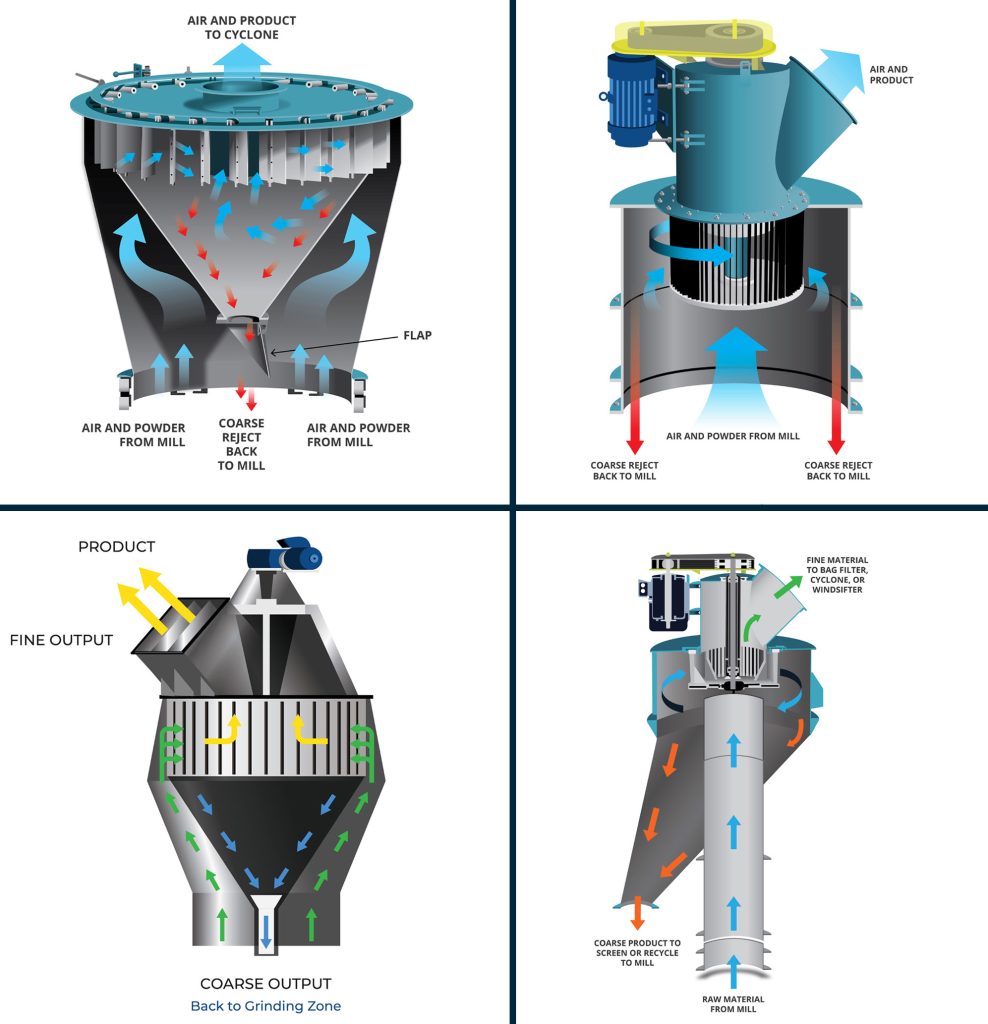
Classifier Efficiencies
All classifiers have an efficiency rating, reflecting how well they separate material. Some are very efficient while others are less so. Inefficient classifiers are unable to achieve a good fine/coarse separation. This means the product stream will contain some coarse particles and the reject stream will contain fine material. This creates additional and unnecessary demand on the mill, resulting in higher recirculation rates which in turn requires more fan pressure and increases the power requirements of the fan drive.
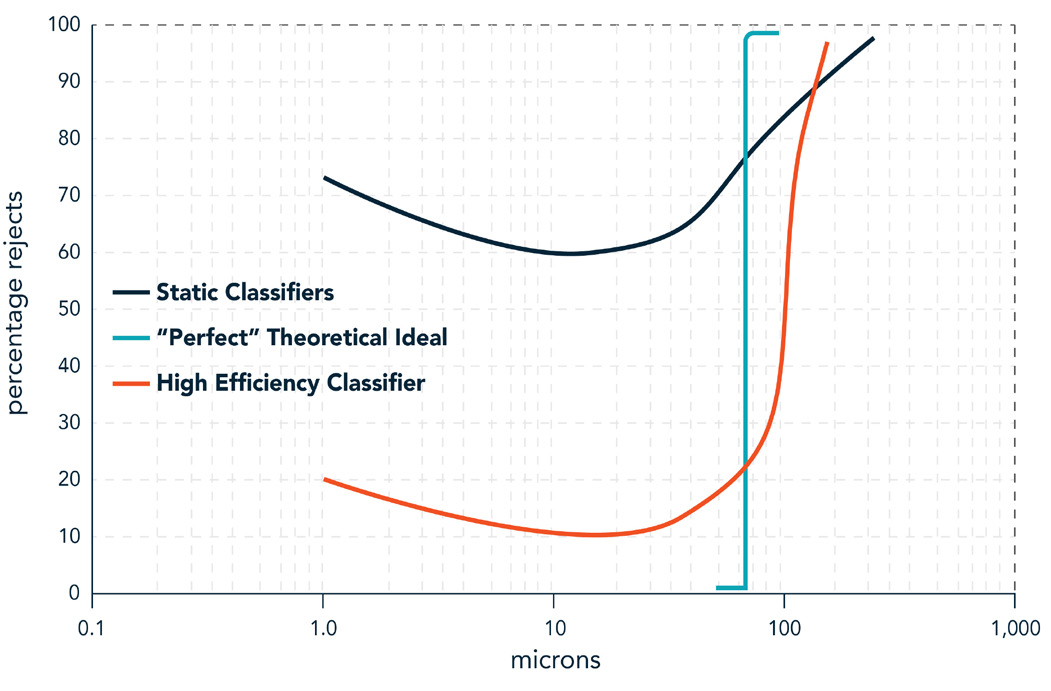
A classifier’s operational efficiency is determined from the ‘tromp curve’ – a graph plotting percentage classifier rejects against particle size. Essentially, this curve shows how much on-size recovery there is in the reject stream. Curves which are as close as possible to a vertical straight line at the cut point are theoretically ideal. Less efficient static classifiers typically show gently sloping lines, whereas more vertical lines – closer to the maximum theoretical limit – are shown by high efficiency classifiers.
Oftentimes, efficiency analyses for existing mill systems will demonstrate opportunities where upgrades to the classifier will improve efficiencies and overall profitability. Upgrading an existing mill system with a new, correctly installed high efficiency classifier can deliver:
- An increase in overall milling system capacity.
- Reductions in power consumption, often up to 8%.
- Sharper classification curves.
Classifiers for the Fertilizer Industry
In the fertilizer industry, dynamic vertical blade classifiers (VBC) are commonly specified for several reasons. VBCs are favoured because they offer high ‘uptimes’ with minimal maintenance and low percentages of rejected particles. They are also relatively low cost and return a quick return of investment (ROI). Dynamic classifiers such as the VBC provide wide flexibility of operation by allowing for instant adjustment of particle separation ranges.
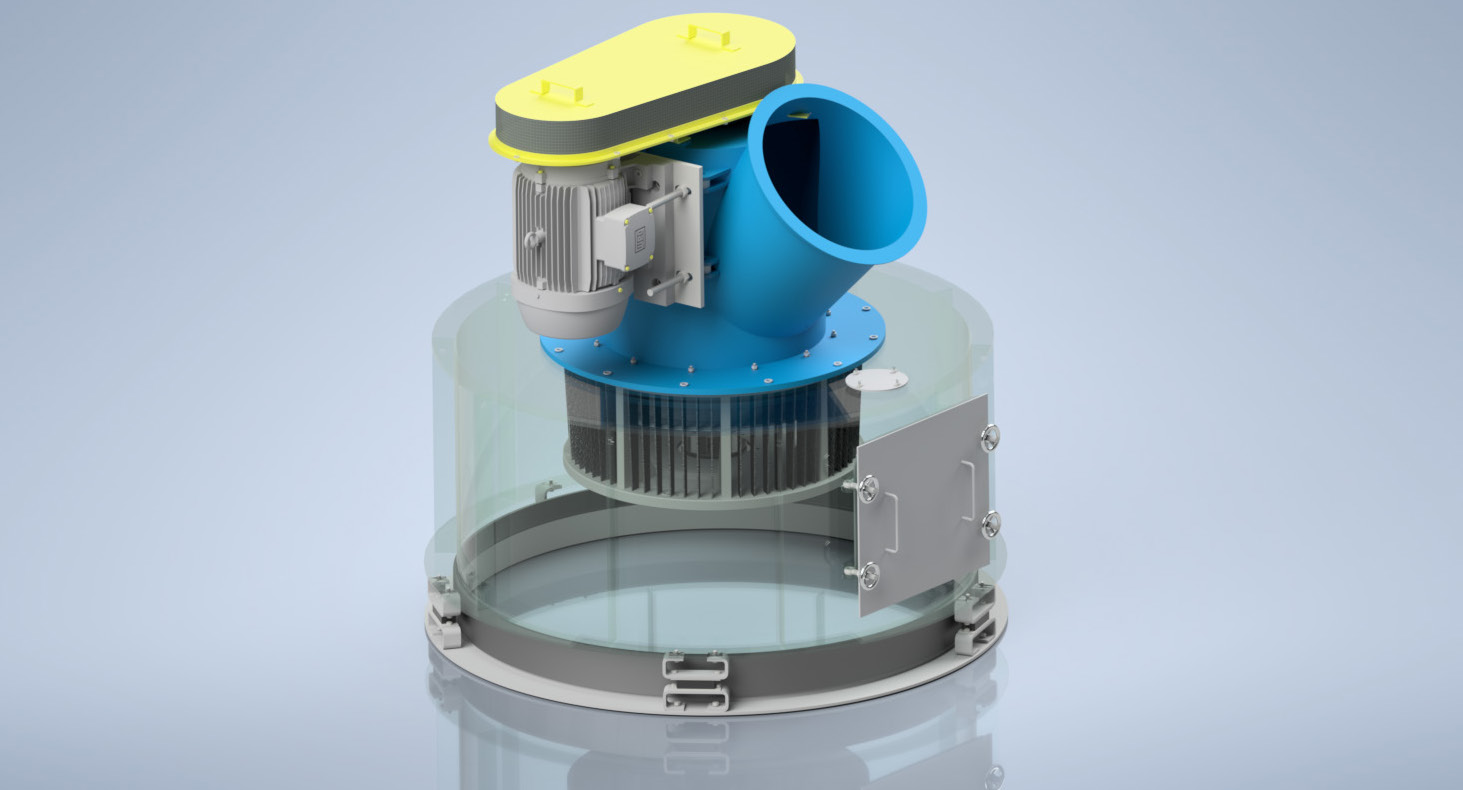
This dynamic classifying technology utilises vertically oriented blades and a separator rotor to create a vortex, spinning the passing air and throwing coarse particles out to the sides of the mill where they fall back into the grinding zone. Desired fine particles are carried out through the separator rotor, and up to the cyclone or bag filter collector. Power reductions result from a reduction in the amount of regrinding that occurs and a lessening of the ‘clouding’ effect that is caused by a mixture of fine and large particles occurring within the grinding chamber with an improperly balanced gas flow.
Another advantage is the ability to automate particle size control when coupled to an inverter (variable speed drive, [VSD]). The product size is controlled by changing the rotor speed. This is done by an inverter drive and can be adjusted with the mill online. This type of separator allows maximum efficiency and stable product size.
Expanded Capabilities with Divorced Classifiers
Demand is on the rise for milling systems with expanded capabilities and improved performance. Divorced classifiers take particle classification outside of the mill’s grinding chamber, which allows for expanded capabilities such as simultaneous production of multiple end products of different size specifications from a single feed continuous processing system. In fact, there are divorced classifiers currently in operation that are simultaneously producing four or more different sized commercial products.
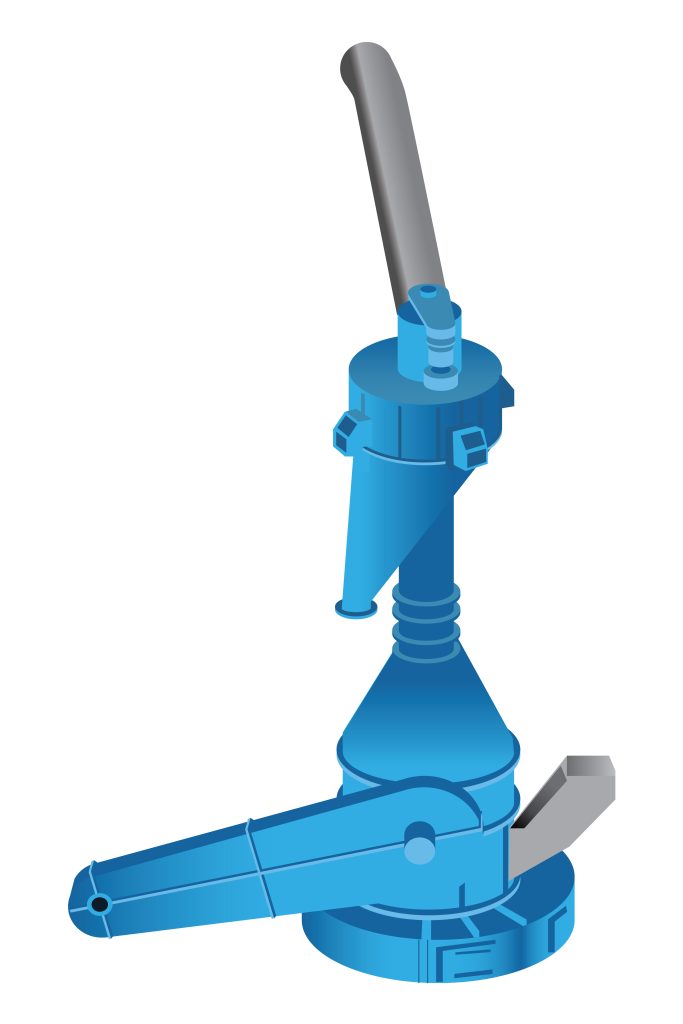
For example, airswept pendulum roller mills are typically employed to pulverise rigid/friable materials into fine powders from 50% passing 150 μm to 99.9% passing 30 μm, whereas vertical shaft impact crushers are employed to crush rigid and friable raw materials to coarse grit specifications. Impact crushers require a capitol cost to purchase and have high energy demands to operate and cannot produce high yields of fine particles. Divorced classification milling systems, on the other hand, can produce high yields of both fine powders and coarse grit in one operation, in one machine, with a much lower demand for energy consumption. In fact, the same amount of power is required to generate fine powders as it is to generate both fine powders and coarse grits. Zero additional power is required to generate two products simultaneously vs just one.
Additionally, divorced classifiers can significantly increase milling efficiencies in fertilizer applications when materials are particularly difficult to grind and/or there is a demand for very fine (<45 μm) product. Mill classifiers lose efficiency when very fine particles are specified because more grinding is required to meet the specification, so more time is required in the recirculating airflow within the mill chamber. The result is an unwanted mixture of particles that hovers in the mill’s grinding chamber consisting of fine particles that are near spec but not heavy enough to fall and are caught in their own airstream midway up the grinding chamber. This ‘clouding’ of particles within the grinding chamber significantly reduces efficiencies and leads to increases in maintenance requirements.
Divorced classifiers alleviate clouding in mill systems by taking particle classification outside of the mill’s grinding chamber, thus creating a one-way flow of air through the mill chamber vs recirculating the airflow within the chamber. After feed materials are ground in the mill chamber, the one-way airstream takes all particles out of the mill to the divorced classifier where fine particles exit to storage while coarse particles are directed back into the mill chamber for further grinding. The result is very often higher profitability from reduced vibration/less maintenance, better particle size consistency, and throughputs up to 15% higher.
Existing milling systems can be converted to divorced classification milling systems relatively easily by reconfiguring the fan and classifier configuration attached to the mill. Furthermore, by combining the Bradley Windsifter classifier to the divorced classification system, up to seven (or more) products of different size can be produced simultaneously.
Classifier Troubleshooting
It is the classifier that ultimately controls a mill’s yield rate and hence the overall profitability of the plant. It is therefore imperative to evaluate both the mill and classifier together as a single system and not independent of one another.
The same ethos applies to post startup problem solving. It is recommended that a structured or holistic approach is taken when troubleshooting production issues, with scrutiny of the process itself to identify the true cause of the problem. After all, the problem that presents itself may well have an indirect cause. If the mill is apparently lacking power, for example, the right solution may not be installing a bigger motor or investing in a new more powerful mill. Instead, the problem could be solved – and often is – by making air flow adjustments at the mill and/or classifier.
Unfortunately, mill systems were not encountered where the classifier was not evaluated properly prior to installation and cannot achieve the yields required to achieve profitability. In such cases, it is still more cost effective to replace the classifier than the mill.
Most problems encountered in milling systems could ultimately have been avoided from the outset if:
- A more thorough evaluation of classification requirements had been carried out pre-purchase.
- There was a better understanding of the process adjustments necessary to achieve maximum yields.
The Future of Classifiers
Many advancements in materials science have been afforded by the ability to grind raw materials down to the elemental level while retaining high levels of purity. For example, pure proteins can be separated from plant fibres at sub 10 μm sizes but currently require unprofitably high levels of energy. Enhancements to classifier technology, such as rotor blade angle configurations that are being researched by Bradley Pulverizer, and are proven to improve efficiencies in milling and classifying processes.
The data collected from this extensive research and testing has been analysed and organised into baseline datasets representing expected performance results from various air classifier configurations. All data has been added to a master database of reference materials and is available as valuable information to reference when engineering future projects.
Optimisation of Milling Systems
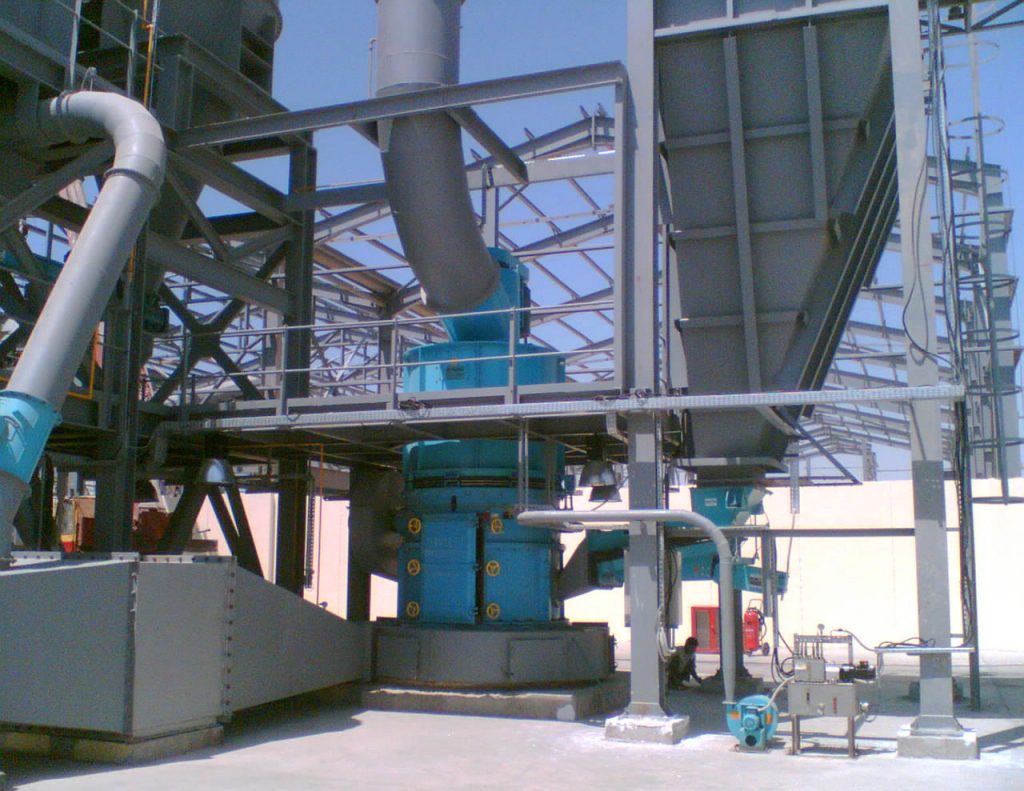
While some milling applications dictate a clear choice of particle classifier, in most cases, selecting the right air classifier involves considering the total cost of ownership, including overall yield rates and system profitability.
Dynamic and divorced classifiers are most commonly used in the fertilizer industry, but classifiers are generally not designed to be industry-specific, and each type can satisfy a fairly wide range of performance specifications such as particle size and shape. After classifier selection, it is critical to evaluate and adjust its settings at the initial project start-up as well as regular maintenance intervals to ensure all product specifications are continuously achieved. Optimisation of the milling system for highest yields, increased efficiencies, and smooth operation begins with an evaluation of the milling system while in operation, followed by material sampling during a hard stop, and analyses of gas/material flows using computational fluid dynamics (CFD) technology.