Grind, Classify, and Dry in One Operation
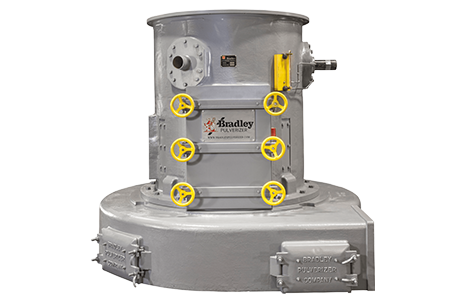
Bradley Airswept Mills combine the fine grinding action of a pendulum roller mill with air stream classifying and fluid bed drying capabilities to produce precisely sized particles for a variety of applications. Sized to meet your application requirements, Bradley Airswept Mill systems are used in a variety of industries and can achieve:
- Outputs of <1 to 150 tons per hour
- Product fineness from 50% passing 150 microns to 99.9% passing 30 microns
- Final products with less than 0.1% moisture from high moisture feeds containing up to 15%
Capacity of a given mill size is dependent on a variety of factors, including:
- Material being ground
- Fineness of the finished product
- Amount of moisture in the feed to the mill
Performance Features
- Unique over-driven design means low investment
- Ground level access to wear parts and low feed
- Less vibration and noise reducing maintenance costs
- Simple solid block foundation
- Gearbox oil does not need cooling
- Fluid bed drying saves 25% on fuel costs
- Belt drive allows optimum speed selection
- Negative pressure air system ensures dustless operation
Grinding, Classifying & Drying in One Operation
Our flagship pendulum roller mills are equipped with three pendulum roll assemblies suspended from a rotating carrier. As the carrier rotates, centrifugal force causes the roll assemblies to swing outward against the stationary ring. Plows direct material from the mill floor to the grinding zone where it is ground using a combination of attrition and impact.
A continuous air stream carries pulverized material from the grinding zone up to a separator. Product sized material is collected while overized particles are rejected and recycled for further grinding. The conveying air stream can also be heated to fluidize and dry material being ground.
Pulverized material from the grinding zone is carried by the air stream up to a separator located above the mill. From there, product size material is carried to a bag house or collection cyclone while oversize particles are rejected and returned to the mill for further grinding.
Bradley Airswept Mills can be equipped with many different styles of classifiers to meet customer application demands. To produce desired particle size distribution, Bradley Pulverizer offers both static and dynamic classifiers.
Learn More About:
For processes that utilize high moisture feed materials, the conveying air stream can be heated for fluid bed drying of ground material. Hot air is introduced into the grinding zone of the mill to fluidize and dry ground particles for easier flow through the airswept system. This method of drying is also advantageous as it reduces costs of drying material.
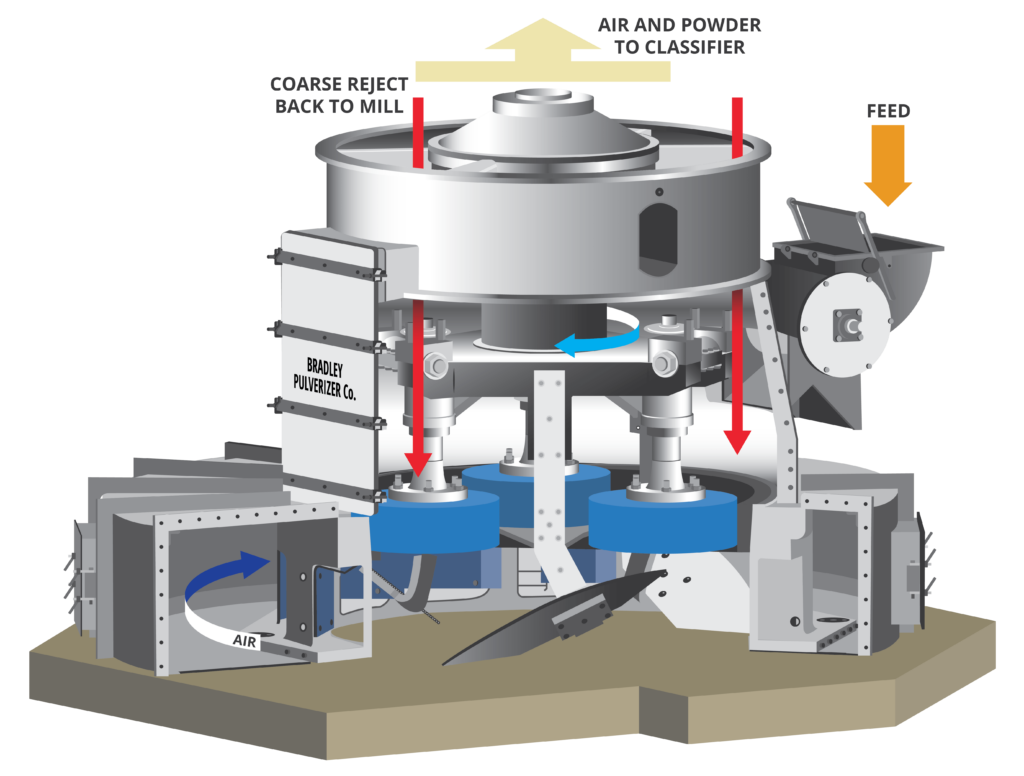
Over-Driven Integral Gearbox Advantages
Bradley Mills are unique among ring-roll designs in that they are driven by an overhead integral gearbox – including our largest sized mills . The Bradley Mill gearbox sits above the grinding chamber which offers several advantages over competitor mills.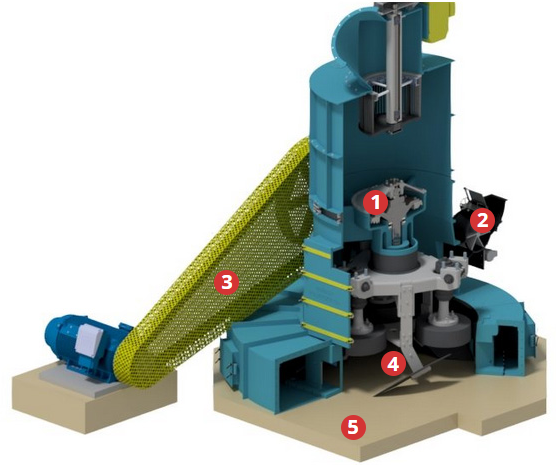
The unique over-driven design of the Bradley Pulverizer Air Swept Mill is more efficient than other mills resulting in a lower per ton operating cost. The mill’s robust construction means lower maintenance costs and less down time than other mills. The drive and gearbox configuration ensures vibration is minimized, operation is quiet and maintenance requirements are kept low for years – decades- of high performance. The end result is a simple, solid foundation with lower installation costs and a superior power-to-weight ratio.
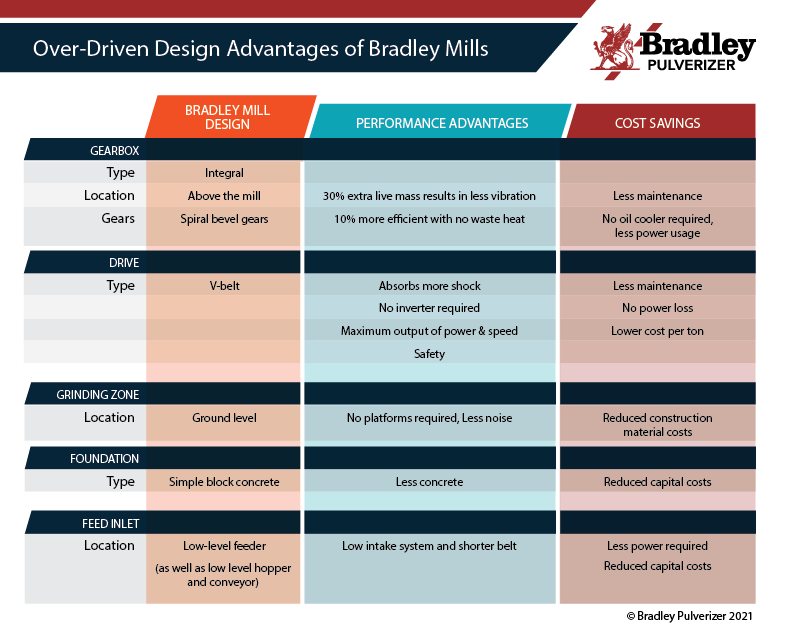
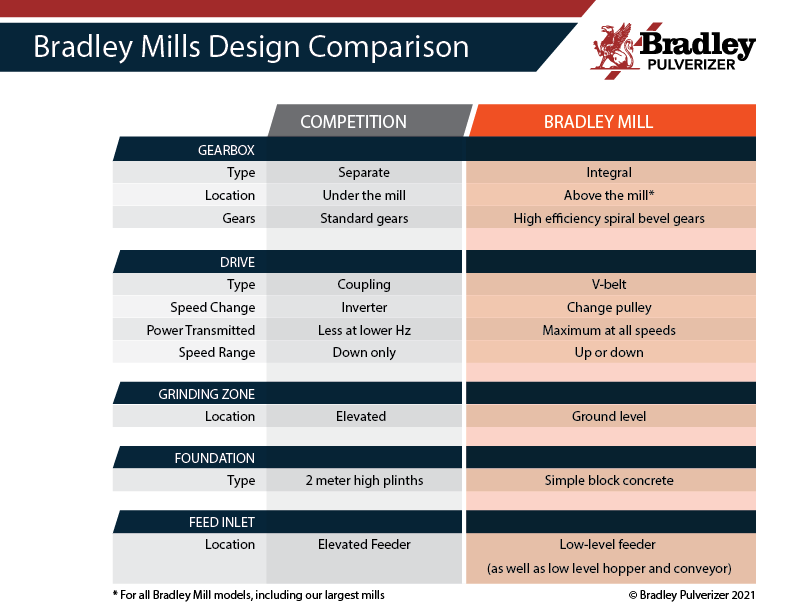
Applications
- Fertilizer Industry
- Cement Industry
- Coal & Coke Grinding
- Limestone & Dolomite Quarries
- Pellet Plants
- Glass & Ceramics
- Mining Industries
- Oil Industry
- Paint Manufacture
- Desulphurization Process
- Marble Processing
- Miscellaneous
Standard Mill Specifications
Mill Size | Mill Motor | Fan Motor | Maximum Feed Size |
---|---|---|---|
BM2 | 22 KW 25 HP |
30 KW 40 HP |
13 MM 0.5 IN |
BM3 | 35 KW 50 HP |
30-35 KW 40-50 HP |
15 MM 0.6 IN |
BM6 | 55 KW 75 HP |
45-55 KW 60-75 HP |
20 MM 0.8 IN |
BM10 | 75-90 KW 100-120 HP |
55-75 KW 75-100 HP |
25 MM 1.0 IN |
BM14 | 132-160 KW 180-200 HP |
90-132 KW 120-180 HP |
30 MM 1.2 IN |
BM20 | 200-315 KW 270-425 HP |
160-200 KW 200-270 HP |
40 MM 1.6 IN |
BM30 | 315-400 KW 425-535 HP |
250-315 KW 335-425 HP |
50 MM 2.0 IN |
BM50 | 400-500 KW 535-670 HP |
375-400 KW 500-600 HP |
60 MM 2.4 IN |
BM60 | 500-750 KW 670-1000 HP |
375-600 KW 500-800 HP |
80 MM 3.1 IN |
Contact Us to learn more about how Bradley Pulverizer can solve your materials processing needs
- Video: Pendulum Airswept Roller Mill
- Video: Airswept Mill Systems
- Case Study: Bradley Mill Overhaul and VBC Upgrade
- Article: The Importance of Phosphate Milling
- Article: Mill Optimizations for Low Grade Phosphate
- Brochure: Airswept Roller Mills
- Brochure: BM00 Airswept Pendulum Mill
- Top Considerations When Selecting a Milling and Classification System
- A Comparison of Mills Used for Phosphate Rock Grinding
- Unique Design Advantages of Bradley Air Swept Roller Mills
- Performance Advantages of Bradley Mills
- Which Airswept Mill is Right for Me: Single-Pass or Recycled System?
- Using a Divorced Classifier to Generate Multiple Products Simultaneously from an Airswept Mill System
- Mills for Phosphoric Acid Manufacturing