Broadfield Process Units
The flexible and reliable design of the Bradley Broadfield Process has been developed from over a century of in-depth process knowledge and experience in SSP manufacturing and other acidulation processes.
This combination of long experience and constantly updated technology is unique, and guarantees high quality product, year after year – this is why Bradley is the preferred supplier for installations the world over.
Complete System Solution
The Broadfield Process can produce SSP economically from all known phosphate rock sources. In reacting phosphate rock, limestone or other minerals with phosphoric or sulfuric acids, the Broadfield Process Unit can tolerate significant changes in feed and product specifications to produce fertilizers, enriched animal feeds and acid salts to meet your product specifications.
The Bradley Broadfield process has also been used successfully to make:
- Triple Superphosphate (TSP)
- Double superphosphate
- Dicalcium phosphate (DCP)
- Diamonium phosphate (DAP)
- Partially acidulated phosphate
- Monocalcium phosphate (MCP)
- Synthetic Gypsum
- Iron Sulphate
- Other acidic salts
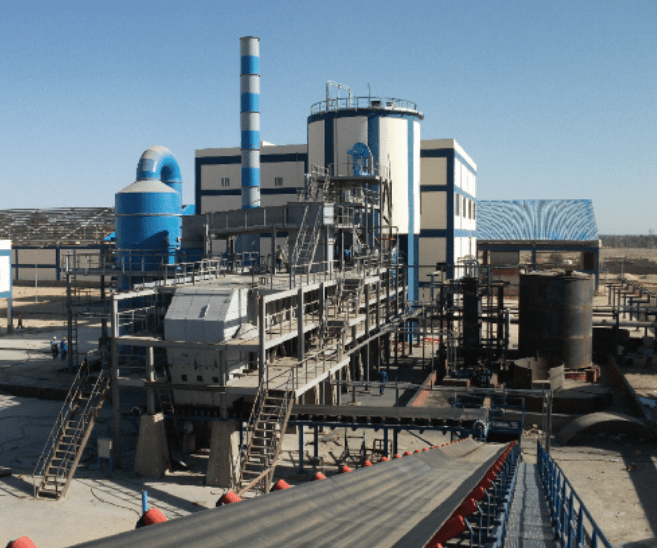
Broadfield Den Features
- Automated feed rate and ratio of acid to feed rates under PLC control
- Specialty mixers promote intimate contact between reactants
- Continuous moving den holds the slurry under suction until it forms a cake
- Rotary cutter shaves product off the cake from the slow moving den
- Belt conveyor moves material downstream to stockpile
- Void scrubbers eliminate reaction gases such as hydrogen fluoride and capture particulates to minimize environmental pollution
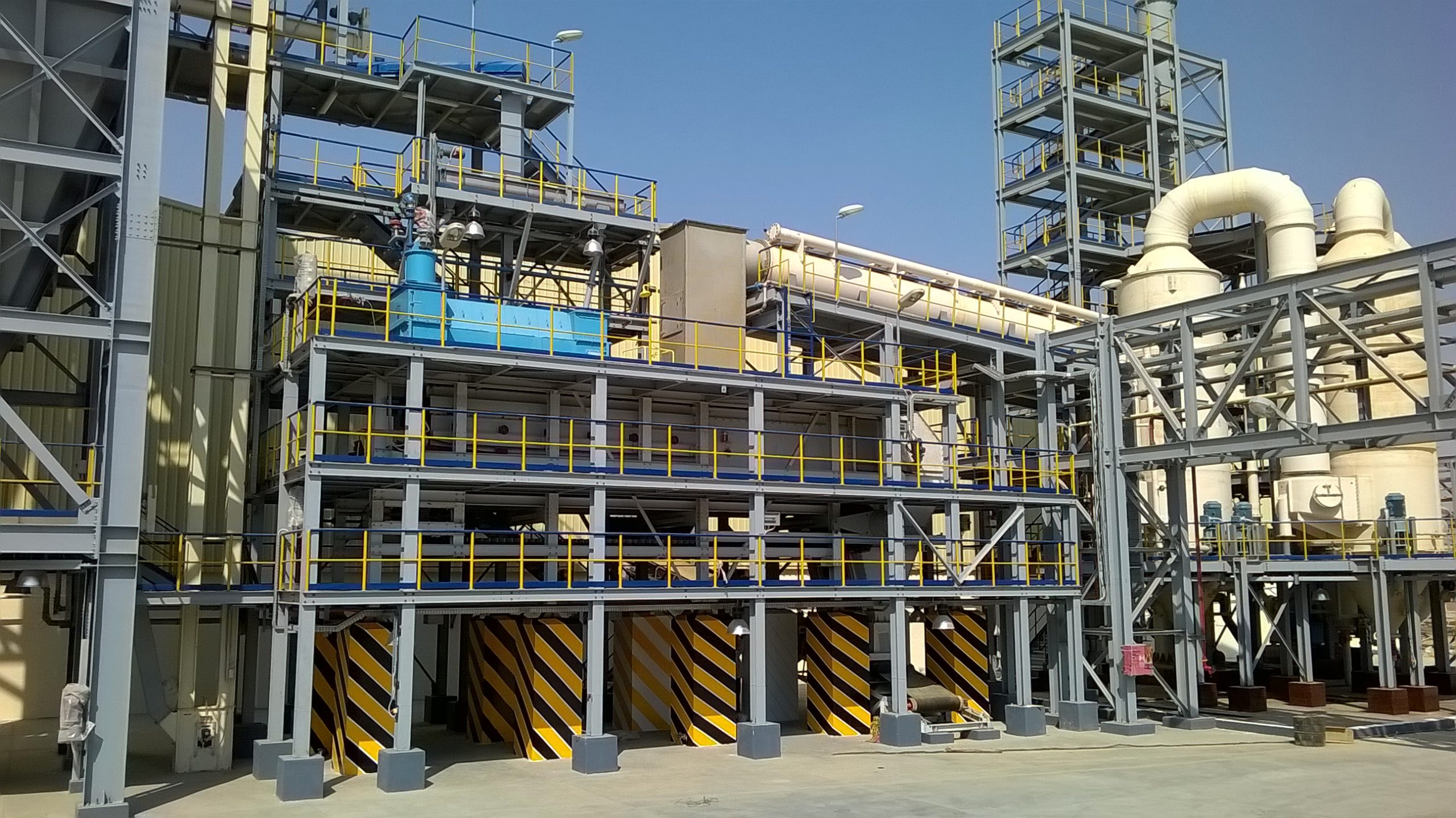
Broadfield Den Design
Mineral rock is ground in a Bradley Airswept Mill to the specified fineness for your material. Material fineness has a direct impact on the reaction rate during the acidulation process and can be easily adjusted in a Bradley mill based on individual differences in rock reactivity.
Raw material is extracted from the feed hopper by a rotary feeder and fed to the mill. The feeder is automatically adjusted to keep the mill motor load constant. In the mill, rollers grind the feed to powder. Air introduced into the mill base carries powder up to the separator, which allows only the correct size particles to pass; oversize particles are returned to the grinding zone.
Ground powder is removed from the air stream in the cyclone and discharged into either the silo or the cyclone screw.
The air from the cyclone is drawn through the mill fan and recycled to the mill. Some of the air is vented to atmosphere via the mill filter to keep the mill under suction.
REACTION SYSTEM:
Mixing of phosphate powder with sulfuric acid or phosphoric acid is carried out in special mixers and a continuous Broadfield Den. Mixer selection is based on several factors, including acid strength used, rock quality, material reactivity and the product being manufactured. Paddle mixers, turbine mixers and cone mixers are typically used for the blending of powdered materials and acid in the Broadfield Process.
Ground rock and an acid solution is added to the mixer where much of the reaction occurs. As a fluid slurry is formed, it is discharged into the den and spreads out and expands to fill it from side to side. The den sides at the inlet end reciprocate to stop the cake sticking to the sides when it is still expanding, and the slurry solidifies to form a cake. The slatted steel den floor moves slowly with adjustable speed set to give a dry, porous cake by the time it reaches the cutter at the outlet end.
The rotary cutter slices material from the cake at the end of the den in the form of a damp powder. The den speed is set to ensure that the powder will not cause blockages on the conveyor belts and to retain material in the den to allow completion of secondary reactions.
SCRUBBER SYSTEM:
A highly efficient scrubbing system is employed to clean the exit gases of dust and fumes prior to discharge. The scrubber fan draws out the gases from the mixer and the den and washes the gas with water to trap the fluoride  and silica components. The gas treatment is performed in multiple  stages to reduce the fluorine content to <5mg F/m3. Recycling hydrofluosilicic acid back to the mixer creates a liquid effluent free plant.
CURING/STORAGE:
The conveyor belts deliver the powder to the stores where the final stages of the reaction, known as curing, take place. This reaction is slow so the acidulated powder is kept in piles to conserve heat. The cut material is stored until ready for final granulation.
Broadfield Process Unit Capacities
Depending on the desired application or plant capacity for your acidulation process, Bradley Pulverizer has the solution:
- Broadfield Den – capacities from 10 to 100 TPH
- Broadfield Belt Den – capacities from 1 to 50 TPH
 | M | L | K | F | E |
---|---|---|---|---|---|
Tonnes per Hour (dry basis) |
10 | 20 | 30 | 70 | 100 |
*All Broadfield Dens are designed run from 60% to 110% of design capability.