
Market: Civil Construction/Limestone Quarry
Application: Grinding of limestone for use in tarmac for road manufacturing
The Challenge: LKAB Minerals needed to increase production rates and reduce maintenance downtime at the Hanson Aggregates Shap Quarry, where limestone is currently ground to 70-75% passing 63 microns for use in tarmac for road manufacturing. Outside of regularly scheduled maintenance, no major updates had been made to the existing Bradley airswept mill for over 13 years, and the mill has been continuously grinding coarse limestone materials for over 43 years.
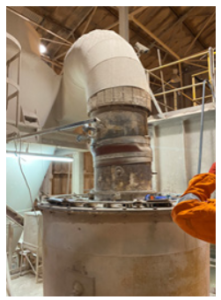
Additionally, the existing mill system needed to process a wider variety of material grades to service a more diverse customer base. Finding a partner who could satisfy all requirements while following CDM guidelines was further complicated by the confined workspace around the mill, short installation time frame, and winter weather conditions.
Increased up-time of the Bradley mill would both improve efficiencies and lower annual production costs.
The Solution: The Bradley Pulverizer team was selected as turnkey manager responsible for all aspects of the project including all risk assessments, securing permits to work with exclusion zones, design and fabrication, installation, start-up, and training. All safe systems of work (SSOW) prepared by subcontractors were submitted to Bradley for conformity and became part of the Bradley safety work file. CDM regulations were followed and documented throughout, and “all work was completed on schedule in extreme weather conditions,” as stated by Lee Dursley, Plant Manager at LKAB.
Vertical Blade Classifer (VBC) Upgrade
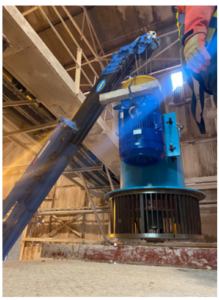
The primary goals of increased production and the ability to process a wider range of material grades were solved by replacing the original static classifer with a vertical blade classifer (VBC). The VBC was selected because of its effectiveness at reducing the circulating load hence reducing the oversize return to the mill for further processing until they meet the required size specification. Early results are impressive with up to 19% increases in output, which equates to almost two-ton per hour higher yield without introducing any additional energy requirements into the system.
Installation of the vertical blade classifer required several ancillary changes to the electrical and control systems of the mill as well as structural modifications due to the confined space in which the system resides. New ductwork and support platforms needed to be built and installed to accommodate the new VBC, while exercising extreme caution to maintain all safety protocols and avoid compromising the integrity of adjacent machinery.
The Bradley Vertical Blade Classifiers (VBC) was also selected because it is equipped with an inverter which enables maximum flexibility on rotor speed to grind multiple products of varying grades. Particle size can be controlled quickly by simply adjusting the separator rotor speed.
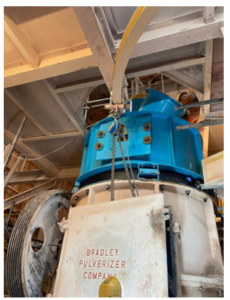
On-Site Mill Overhaul
The mill’s first major overhaul in over 13 years accomplished improvements in mill reliability and increased up-times. The mill mechanics were stripped down and rebuilt on-site, including a rebuilt gearbox for much-improved oil retention. The existing roll carrier was retrofitted with new rolls and re-installed. Further mechanical upgrades included a new motor for the VBC. New cabling and switch gear was added to meet current electrical UK regulations. All-new controls were integrated into the existing motor control cabinet for a more user-friendly experience for the machine operator.
Bradley Training and Support
Post-installation support included training for mill operators following COVID guidelines for running the new VBC. A maintenance guide was provided with daily, weekly, and monthly guidelines to follow and Bradley has been contracted to provide biannual maintenance on-site.
Benefits: Post-installation support included training for mill operators following COVID guidelines for running the new VBC. A maintenance guide was provided with daily, weekly, and monthly guidelines to follow and Bradley has been contracted to provide biannual maintenance on-site.
- 19% increase in yields
- Overall performance improvements
- Reduction in maintenance and downtime
Contact Us to learn how Bradley Pulverizer can overhaul and upgrade your milling system to increase productivity and decrease operating costs.
(US) 855-670-8777 | (International) 0808-196-8141