Mill Optimizations for Low Grade Phosphate

Milling Rock for Phosphate Fertilizer
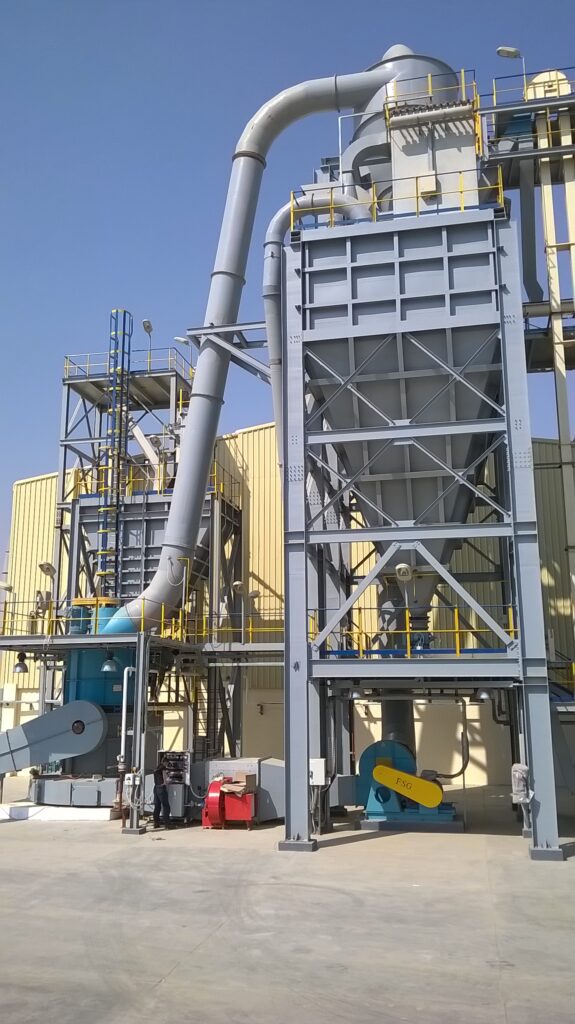
Phosphate rock is fed into the front-end of a fertilizer production plant and manipulated many times during its process journey, eventually transforming into valuable fertilizer end-products. Maintaining continuous production rates with minimal downtime across the variety of interconnected machinery is essential to profitable phosphate fertilizer manufacturing.
The production process begins with the pulverisation and grinding of phosphate-rich rock in an airswept pendulum roller mill. The resultant powder is then fed into downstream processes for acidulation, mixing, and pelletizing through to final packaging. Every item of process equipment is interdependent, with the entire plant functioning as an interconnected network. In many ways, it is the upstream milling of phosphate rock that ultimately drives plant profitability and the overall quality and yield of the end-product.
The continuous nature of the fertilizer production process means that adjustments to one piece of machinery will almost always require adjustments to other equipment. Relatively expensive retrofits and re-engineering costs to downstream processing machinery can be minimised by effectively optimizing the upstream milling equipment, ensuring that it continues to generate phosphate powder that meets the required specifications for downstream production.
Comparing High Grade to Low Grade Rock
Historically, sedimentary rock with over 30% P2O5 content and SiO2 as low as 4% has been considered “high-grade” due to its high phosphate content, low silica content, and the relative ease of grinding compared to igneous rock. Worldwide sources of high-grade sedimentary apatite are decreasing due to historical demand, though phosphate-rich igneous rock offers an alternative source for phosphate fertilizer producers. Igneous rock grinding and pulverizing, however, creates challenges to the machinery required to meet mineral product specifications. The challenge of igneous versus sedimentary rocks is nothing new in the fertilizer production industry. While sedimentary rock is softer and easier to pulverise in a mill, it contains levels of heavy metals such as cadmium, which often exceed the generally accepted required limit of <280ppm in the end-product. Igneous rock is commonly mixed with sedimentary rock to minimise the levels of heavy metals while still meeting commercially viable levels of phosphate in the fertilizer.
Because igneous rock has a tighter crystalline structure than sedimentary rock, it requires longer grinding times to expose greater particle surface area and meet particle cut size specifications for optimal processing. Furthermore, igneous rock contains higher levels of the abrasive mineral silica. While silica does not have negative environmental implications or impact the chemical reactions within the fertilizer process, it is highly abrasive and results in higher rates of wear on the mill and the overall milling system.
Low Grade Rocks | High Grade Rocks | |
---|---|---|
Phosphate (P2O5) levels in rock | 17 – 27% | >27% |
Silica levels in rock | Higher | Lower |
Contaminants in rock | Higher | Lower |
Mechanical Wear on mill | Higher | Lower |
Particle size | Finer | Less Fine |
Throughput | Lower | Higher |
Optimizing Mill Systems for Low Grade Rock
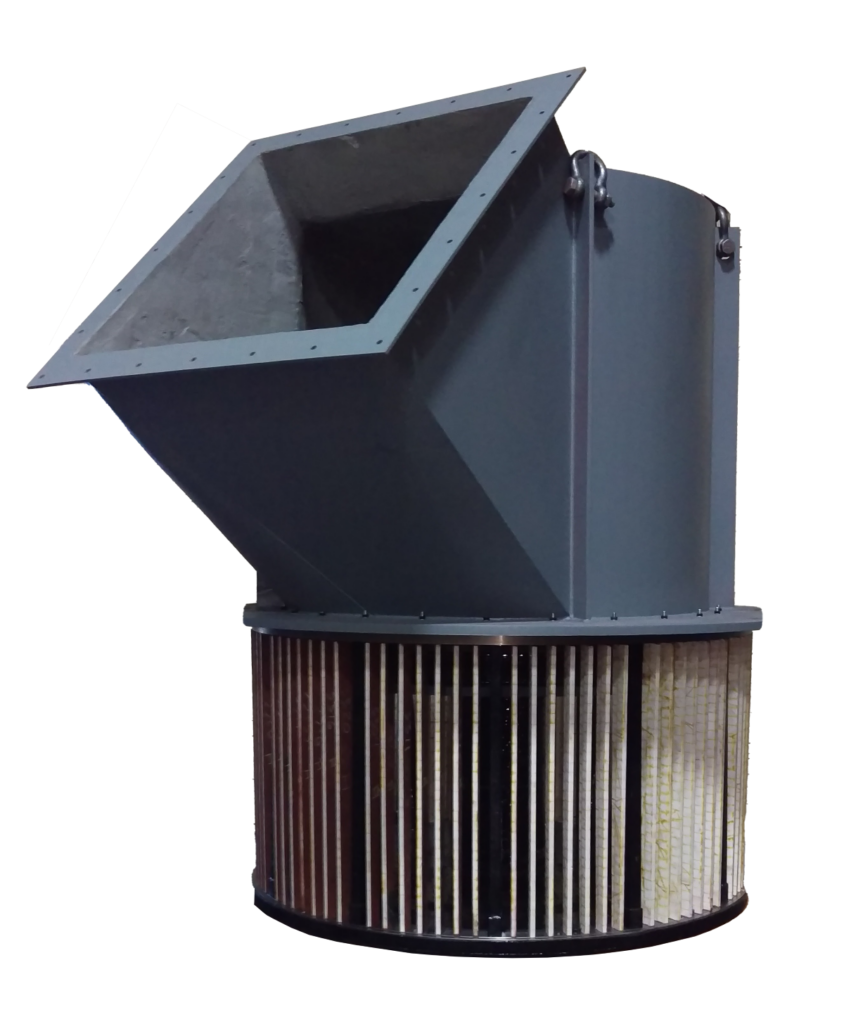
While technology and design have advanced over the years, the general function of Bradley mills to provide continuous grinding of hard friable minerals has remained relatively unchanged since first being used for fertilizer production in 1873. The mills are engineered for operating at lower speeds to reduce the degree of wear commonly encountered from high impact milling, with a key design feature being the ability to custom enhance the wear resistance of the mill and system. A wide array of options are available to ensure the best long-term solution is established to fit the application and feedstock of the process.
The grinding chamber within the mill where minerals are pulverized between the grinding rolls and the grinding ring is where the most aggressive action occurs. High levels of wear are to be expected in the grinding chamber, and there are ways of mitigating this wear with advanced alloys for the grinding rolls and ring, which provide longer life and more continuous running.
Mechanical components such as the gearbox, grinding chamber, carrier, and rolls can all be lined for protection and added life as well. Rubber lining is particularly cost-effective when properly monitored, as re-coating of worn linings is much more economical than a complete replacement of mechanical components such as gearboxes. Mill classifiers are also susceptible to higher abrasion and wear within the mill system. Solutions include lined casings with alumina tiles and rotors lined with rubber or titanium spray. In extreme wear conditions, chrome carbide plate has been used.
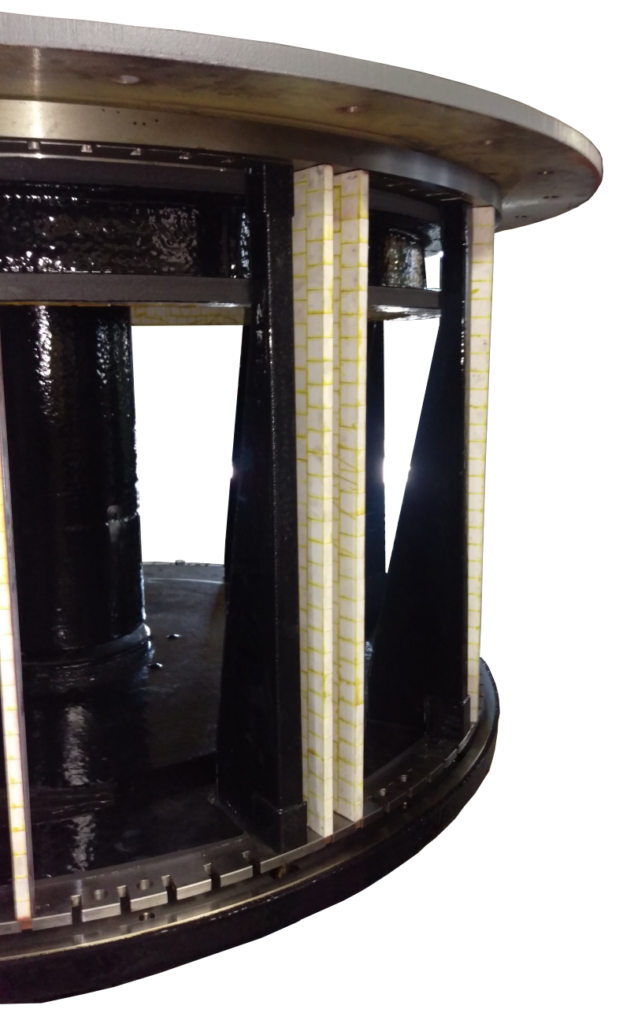
Ancillary equipment and ductwork throughout the mill system are not immune to the erosion from pulverized rock and silica being conveyed throughout. The internals of the mill system itself can be protected with wear protection material as needed. If issues result from direct impact, rubber-based material works very well for lining cyclones and ducts. If impact has a scouring effect within the system, hard material such as Hardox abrasion-resistant plate can be used, and chrome carbide is recommended in extreme conditions.
Additionally, ceramic coatings are available for components exposed to extreme wear, which provide a hard, wear-resistant surface that can greatly reduce the rate of wear in high-stress areas. This technology is particularly useful for protecting classifier components and other ancillary equipment.
Bradley Pulverizer’s wear enhancement options are part of a comprehensive approach to optimizing milling systems. Analysis of the specific conditions and challenges of each milling operation results in a tailored combination of wear-resistant materials and technologies to ensure that every aspect of the milling system is optimized for maximum efficiency and longevity.
Summary
The pulverization of phosphate-rich apatite rock to particles small enough for chemical reactivity is the most critical step in the production of phosphate fertilizers. Production-scale manufacturing requires mass pulverization of rock without the ability to separate the economically beneficial phosphorus from the other minerals present, such as silica, aluminum, and cadmium. Therefore, rock mixtures must be selected based on their mineral makeup to provide commercially viable volumes of phosphate without exceeding safe levels of heavy metals.
Historically, sedimentary rock has been preferred due to lower processing times and less machine wear. However, the declining availability of high-grade sedimentary rock now necessitates the use of more igneous rock in the process. Harder igneous rock with more silica requires more processing time and imparts higher levels of wear on the milling machinery.
To counteract the effects of processing igneous rock, Bradley Pulverizer has established several methods for enhancing mill and mill system wear resistance. These include rubber linings and abrasion-resistant plates installed at known areas of high wear. These options extend the life of the equipment and minimize downtime. Additionally, they can be custom configured to meet the demands of the material and the fertilizer processing system, ensuring continued high efficiency and profitability in the production of phosphate fertilizers.