Ian Hancock, Bradley Pulverizer, UK, discusses several machine wear enhancement options for mills, classifiers, and milling systems for phosphate fertilizer production. Click Here to download the complete article in pdf format as published by World Fertilizer Magazine – Oct 2024, pp. 31-33.
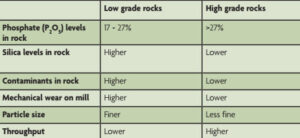
While technology and design have advanced over the years, the general function of Bradley mills to provide continuous grinding of hard friable minerals has remained relatively unchanged since first being used for fertilizer production in 1873. The mills are engineered for operating at lower speeds to reduce the degree of wear commonly encountered from high impact milling, with a key design feature being the ability to custom enhance the wear resistance of the mill and system.
The grinding chamber within the mill where minerals are pulverized between the grinding rolls and the grinding ring is where the most aggressive action occurs. High levels of wear are to be expected in the grinding chamber, and there are ways of mitigating this wear with advanced alloys for the grinding rolls and ring, which provide longer life and more continuous running.
Mechanical components such as the gearbox, grinding chamber, carrier, and rolls can all be lined for protection and added life as well. Rubber lining is particularly cost-effective when properly monitored, as re-coating of worn linings is much more economical than a complete replacement of mechanical components such as gearboxes. Mill classifiers are also susceptible to higher abrasion and wear within the mill system. Solutions include lined casings with alumina tiles and rotors lined with rubber or titanium spray. In extreme wear conditions, chrome carbide plate has been used.
Ancillary equipment and ductwork throughout the mill system are not immune to the erosion from pulverized rock and silica being conveyed throughout. The internals of the mill system itself can be protected with wear protection material as needed. If issues result from direct impact, rubber-based material works very well for lining cyclones and ducts. If impact has a scouring effect within the system, hard material such as Hardox abrasion-resistant plate can be used, and chrome carbide is recommended in extreme conditions.
Additionally, ceramic coatings are available for components exposed to extreme wear, which provide a hard, wear-resistant surface that can greatly reduce the rate of wear in high-stress areas. This technology is particularly useful for protecting classifier components and other ancillary equipment.
Wear enhancement options are part of a comprehensive approach to optimizing milling systems. Analysis of the specific conditions and challenges of each milling operation results in a tailored combination of wear-resistant materials and technologies to ensure that every aspect of the milling system is optimized for maximum efficiency and longevity.
Contact Us if you are running into issues with reduced performance due to low grade rock and we will evaluate possible solutions to improve performance.